Redefining sustainable logistics
The innovation project in Bålsta is one of our three so-called Earth Shot projects aimed at exploring different ways to reduce the carbon footprint of the built environment. The project is redefining the logistics sector by minimizing the carbon footprint of both materials and operations, while also focusing on aesthetics, well-being, and biodiversity.
To our knowledge, this is the world’s largest hemp-insulated logistics building and the first to use bio-based materials on a large scale throughout its construction – something that has reduced carbon emissions by 88% compared to traditional methods and materials. Drawing inspiration from NASA’s space innovations, the project combines sustainability with innovative architecture.
Targeting BREEAM Outstanding, the project sets a new global standard for sustainable construction with a total carbon footprint of only 2.7 kgCO₂/m²/year.

Challenging traditional methods and materials
A key innovation is the development of wooden wall panels with locally sourced hemp insulation, designed to be maintenance-free for at least 50 years.
Beyond its superior thermal performance, hemp insulation captures carbon during growth, further reducing the building’s lifecycle emissions.
An industrial process was developed under the project to produce this product, making it now available in the market.
The building’s modular structure allows for disassembly and relocation, further paving the way towards a more sustainable future. Wooden components make it easy to adapt roof heights or modify the layout for new sites, reinforcing the facility’s circular design principles.
Foundations and floor slabs incorporated low-carbon concrete. A thinner-than-usual concrete slab design reduced material use by 70% compared to standard logistics facilities.
Custom-developed low-carbon hexagon paving stones, with an 80% carbon reduction compared to the traditional option of a concrete plate, were installed in front of the loading docks. These stones demonstrate how supply chain collaboration can lead to scalable sustainable solutions.
Asphalt for outdoor areas was created using recycled linseed oil, replacing traditional bitumen to significantly lower carbon emissions.
Energy efficiency
Solar panels covering the entire roof work in concert with ground-source heat pumps and battery storage, creating a largely self-sufficient energy system.
A state-of-the-art geothermal heat pump uses CO2 as a cooling medium, avoiding the harmful refrigerants typically used in such systems.
Onsite batteries store excess solar energy, which can be used to avoid peak grid demand or power electric vehicle charging stations. These systems lower tenant operating costs and offer a compelling financial incentive for higher rents.
Through these measures, tenants can achieve substantial energy savings. For example, annual electricity costs could be reduced from €100,000 to €10,000, underscoring the long-term financial viability of sustainable investments.
Promotes well-being and biodiversity
Thoughtfully landscaped outdoor areas, including a stormwater pond, pavilion and lush greenery, enhances visual appeal while promoting employee well-being, social interaction and productivity.
The landscaped areas have been optimized to support the natural recovery of the preexisting local flora. Additional perennials have been planted to promote biodiversity, while open ponds and flowering shrubs provide food and habitat for amphibians, birds, and insects.
Inside, the wooden structure plays a vital role in shaping a comfortable work environment. It ensures excellent air quality and optimal acoustic comfort, while fostering a warm, tranquil atmosphere that supports focus and collaboration.
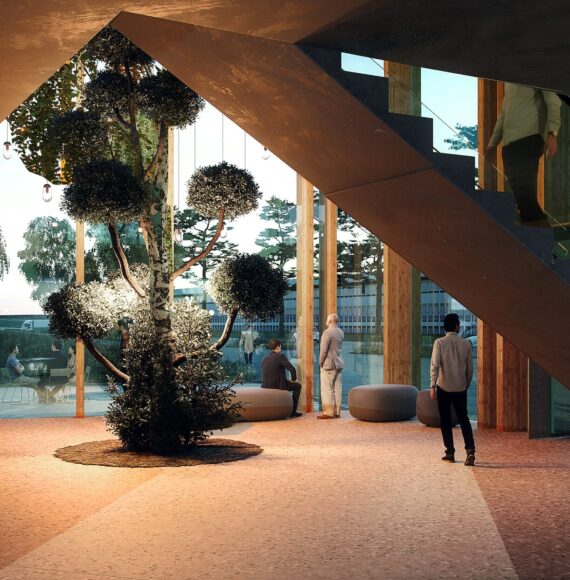
Project summary
PROJECT TYPE: Logistics
LOCATION: Bålsta in Håbo municipality, a short 50 km drive west of Stockholm
SIZE: Altogether 20 845 square meters, including warehouse and office spaces
COMPLETION: 2024
ARCHITECT: Equator
SUSTAINABILITY PROFILE: Awarded by Sweden Green Building Council as the Best Zero CO2 project, 2024. Targeting a BREEAM Outstanding certification.